CUTTING-EDGE POLYCRYSTALLINE DIAMONDS
FOR DIVERSE MACHINING NEEDS
SPR’s PCD range includes a wide variety of material types and grades for almost every application machining nonferrous metals and other non-metallic materials. We welcome discussions on special orders and non-standard grade items. With over 40 years of experience supplying polycrystalline diamond to tool manufacturers, we deeply grasp our customers’ requirements.
Our PCD materials are meticulously crafted to deliver peak performance in every application, empowering diamond tool producers with versatile solutions to exceed their customers’ expectations.


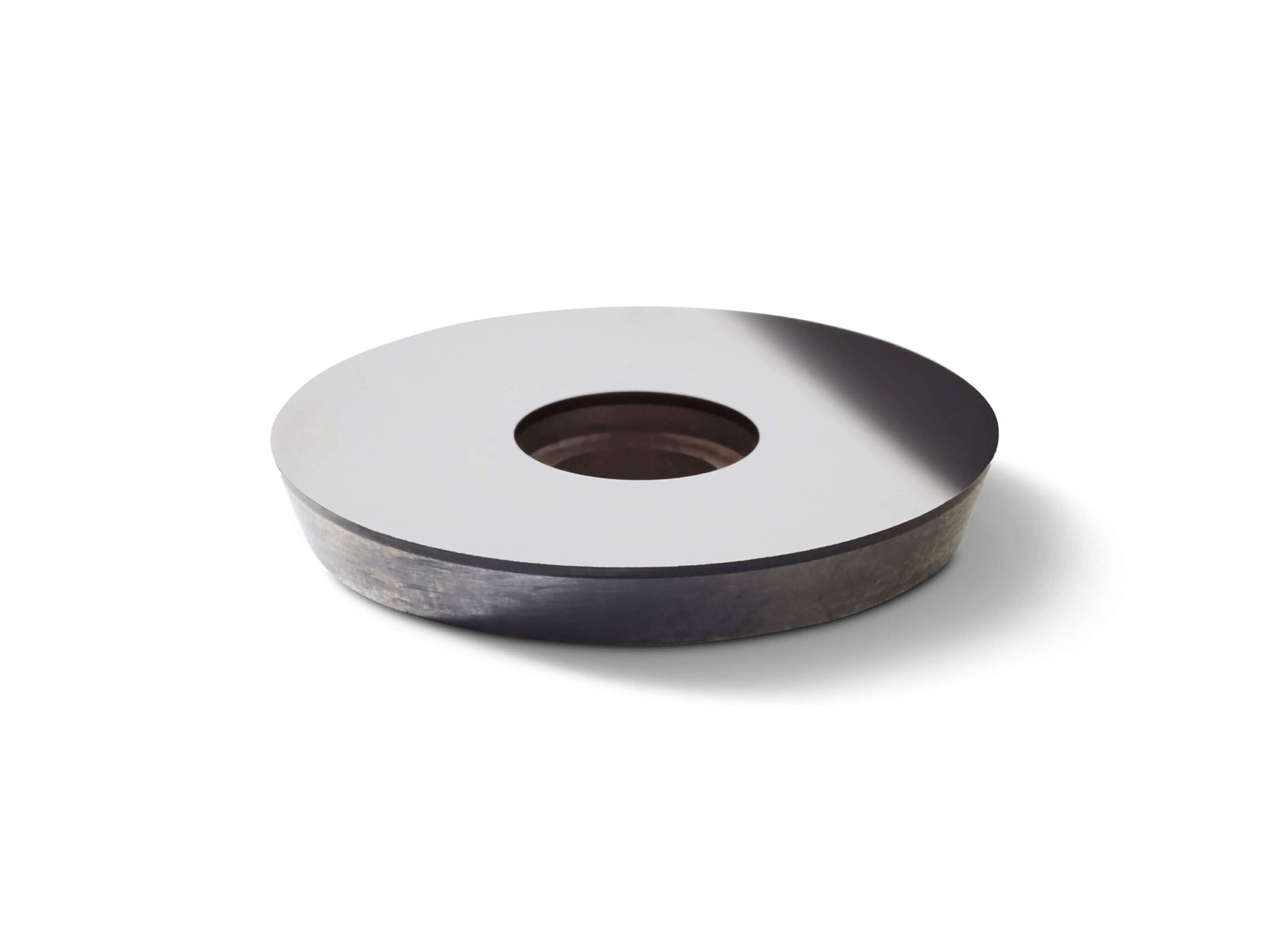
PCD BENEFITS
Our PCD diamond blanks offer a combination of high hardness, abrasion resistance, low friction, and impact resistance. These blanks feature a tungsten carbide substrate that provides mechanical support to the diamond abrasive layer, boosting impact strength and enabling easy braze attachment during tool fabrication.
Widely used in machining non-ferrous and non-metallic materials, PCD cutting blanks have become the global industry standard for superior part quality and significant cost reductions throughout the production cycle.
Unlock the following advantages by incorporating PCD cutting blanks into your
machining process:
-> Achieve higher material removal rates and optimized cycle times, resulting in increased parts per shift.
-> Experience cutting speeds that surpass those of traditional cutting tools, enhancing overall productivity.
-> Attain exceptional workpiece quality with precise dimensional control, consistent surface finishes, and reduced scrap.
-> Enjoy longer tool life, leading to improved machine uptime and increased production capacity without the need for additional equipment investment.
-> Discover the power of PCD cutting blanks and elevate your machining capabilities to new heights.
POLYCRYSTALLINE DIAMOND (PCD)
Grade | Size | Description |
---|---|---|
SUF | sub <1 μm | Ideal for achieving mirror like superior surface finishes in a wide range of non-ferrous applications, including machining mid-high silicon aluminum alloys. Lower cutting force than larger micron materials |
FGS2 | 2μm | Exceptional durability, abrasion resistance, and precise machining capabilities. Ensures superior surface finishes with long-lasting performance. Applications include poly carbon materials and plastics. |
FGS | 5μm | Highly durable impact and abrasion-resistant material, perfect for finishing and high-precision applications. Offers optimal performance and reliability across various industries including wood & composites. |
MGS | 10μm | An optimal blend of durability and wear resistance, suitable for roughing and finishing non-ferrous metals like low silicon content aluminum alloys. |
CGS | 25μm | Super wear-resistant and thermally stable, making it ideal for ceramics, resistant alloys in aerospace, and wind power systems composites. |
CGM | 2-30μm | Multi-model blended PCD makes exceptional wear and impact resistance along with thermal stability for a wide range of applications including woodworking, high silicon aluminum alloys, carbon fiber composites, metal matrix composites, and ceramics. |
Sandwich High-Performance Drill Material
The PCD Sandwich is a high-performance drilling solution. It consists of a PCD layer sandwiched between tungsten carbide layers on both the top and bottom sides. This innovative tool is widely used in drilling applications, delivering exceptional results. Invest in
Sandwich PCD for efficient and effective drilling operations.
T : Blank thickness
t : Diamond layer thickness
Sandwich PCD Grades | Blank thickness (T) | Diamond layer thickness (t) |
---|---|---|
FGS | 1.5mm ±0.05 | 0.5mm ±0.10 |
MGS | 2.0mm ±0.05 | 0.8mm ±0.10 |
CGS | 2.5mm ±0.05 | 1.0mm ±0.10 |
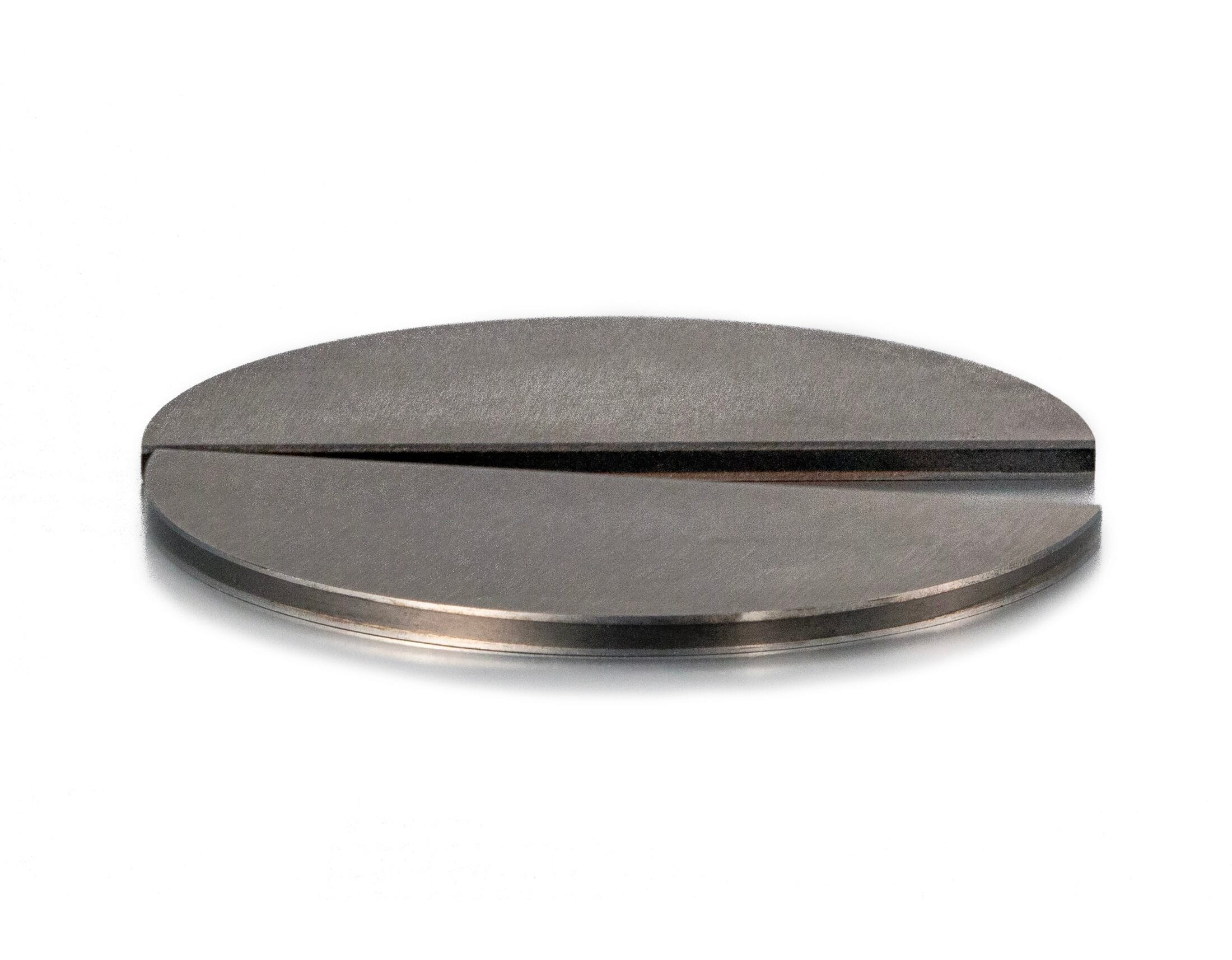
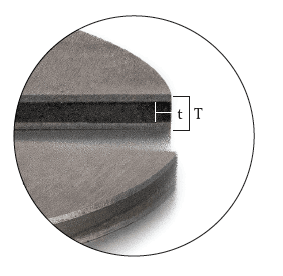

Wood Machining PCD
Achieving Cost-Effective Diamond Tooling Solutions
Over the past few decades, the cost of diamond tools has significantly decreased, making them more accessible and cost-competitive. By examining every step of the manufacturing process and optimizing tool design, you can maximize productivity and achieve the highest level of cost-efficiency.
SPR off ers exceptional Polycrystalline Diamond (PCD) solutions that empower
toolmakers and endusers alike. Our PCD solutions deliver improved competitiveness,
enabling you to enhance your woodworking operations and drive success.
Applications include CFRP, MDF, natural wood, particle board, fi ber glass, plastics and graphite.
Cost-Effective PCD Grade | Size | Description |
---|---|---|
FGW | 2μm | Exceptional strength, abrasion resistance, and precise machining capabilities. Ensures superior surface finishes with long-lasting performance. |
MGW | 10μm | An optimal blend of durability and wear resistance, suitable for roughing and finishing non-ferrous metals like low silicon content aluminum alloys. |
CGW | 25μm | Super wear-resistant and thermally stable, making it ideal for ceramics, resistant alloys in aerospace, and wind power systems composites. |
MACHINING PARAMETER GUIDELINES
MATERIAL MACHINED | OPERATION | PCD GRADE | SPEED (m/min) | FEED RATE (mm/rev) | DOC (mm) |
---|---|---|---|---|---|
ALUMINIUM ALLOY | |||||
4 – 8% Si | Turning | FGS / FGSW / MGS | 900 – 3500 | 0.1 – 0.4 | 0.1 – 4.0 |
Milling | 1000 – 5000 | 0.1 – 0.3 mm/insert | 0.1 – 3.0 | ||
9 – 14% Si | Turning | MGS / CGS / FGSW / CGM | 600 – 2400 | 0.1 – 0.4 | 0.1 – 4.0 |
Milling | 700 – 3000 | 0.1 – 0.3 mm/insert | 0.1 – 3.0 | ||
> 14% Si | Turning | MGS / CGS / CGM | 300 – 700 | 0.1 – 0.4 | 0.1 – 4.0 |
Milling | 400 – 900 | 0.1 – 0.3 mm/insert | 0.1 – 3.0 | ||
METAL COMPOSITES | |||||
AL (10 – 20%) SiC | Turning / Milling | CGS / CGM | 300 – 600 | 0.1 -0.4 | 0.2 – 1.5 |
COPPER ALLOYS | |||||
Copper, Zinc, Brass | Turning / Milling | FGSW / MGS | 400 – 1260 | 0.03 – 0.3 | 0.05 – 2.0 |
TUNGSTEN CARBIDE 10 – 16% Co | |||||
Unsintered (“Green”) | Turning | CGS / CGM | 50 – 200 | 0.1 – 0.4 | 0.1 – 1.0 |
Sintered | Turning | CGS / CGM | 20 – 40 | 0.1 – 0.25 | 0.1 – 1.0 |
CERAMICS | |||||
Unsintered (“Green”) | Turning | CGS / CGM | 50 – 200 | 0.1 – 0.2 | 0.1 – 1.0 |
Sintered | Turning | CGS / CGM | 20 – 40 | 0.1 – 0.2 | 0.1 – 0.5 |
MANUFACTURED WOOD | |||||
MDF | Routing | FGSW / MGS | 1000 – 3650 | 0.1 – 0.4 | 0.1 – 4.0 |
Particle Board | Sawing | MGS / CGS | 1500 – 4000 | 0.5 – 6.0 | 1.0 – 200 |
Routing / Sawing | CGM | 1000 – 4000 | 0.1 – 0.4 | 0.1 – 3.0 | |
PLASTICS / COMPOSITES | |||||
Carbon / Graphite | Turning / Milling | MGS / CGS / CGM | 300 – 2000 | 0.05 – 0.3 | 0.1 – 3.0 |
Fiberglass / Plastics | Turning / Milling | MGS / CGS / CGM | 200 – 1000 | 0.05 – 0.5 | 0.1 – 3.0 |
Fiberglass / Graphite | Turning / Milling | CGM | 300 – 1000 | 0.1 – 0.4 | 0.1 – 3.0 |